Anatomy of an Epoxy Sandwich board
Cores are Styrene-based foams, commonly (and erroneously)
referred to as "Styrofoam", either beaded (the majority, bigger
boards have vent screws), or extruded (a bit heavier). Throughout this site, I
will refer to this material as "EPS", expanded polystyrene, and "XTR",
extruded polystyrene foam.
Because EPS and XTR foams melt with exposure to Styrene, boards
are put together with an Epoxy, most of which have no solvents. Painted boards
use "normal" Epoxies, while clear-finished boards use (or should use)
UV-resistant Epoxies. There are many different Epoxy formulations for special
applications. Most repair jobs will use room-temperature-cure. All Epoxies have
a very specific mixing ratio of resin to hardener, and deviating substantially
from this mixing ratio will make for a gooey mess. Unlike Polyester resins, which
can be accelerated by adding more catalyst, Epoxy resins can only be accelerated
by using a faster hardener (or by heating them - but that's a different story).
Reinforcements (the stuff that provides the strength) are
either fiberglass of some type or another, or Carbon, or KevlarŪ, or combinations
thereof. Fiberglass is an all-around material that does nothing particularly
well, but has no glaring shortcomings, either. Carbon is enormously stiff for
its weight, but quite weak in impact. KevlarŪ handles impacts extremely well, but
is an utter pain to work with. All these reinforcements come in a variety of
arrangements, from random chopped-strand-mat, to woven cloths, to
unidirectional tows. Some combine different raw materials, to tailor the
composite to best handle particular loads.
To improve panel stiffness (decrease heel denting and
such) most boards these days have some sort of sandwich structure. This will
consist of either a linear or cross-linked PVC foam (Airex or Divinycell,
respectively), or wood veneer inserts, or a combination thereof. A cheap
substitute is Coremat, a blanket-like material that absorbs much resin to gain
bulk and stiffness. I don't see many boards with it anymore. Honeycomb cores
were en vogue for a while, but have - fortunately - fallen from favor
recently, due to their propensity to take on prodigious amounts of water.
Where major local loads need to be accommodated, all
boards have (or should have) inserts surrounding the fixtures. These inserts are
commonly made from Divinycell or high-density Urethane foam.
Finish is either resin (most commonly a Polyester finish
resin - beautiful gloss but chips easily), or paint (Epoxy paints are most
common in production boards, while customs usually have Linear Polyurethane
paints - tough and long-lasting), or ASA plastic skin (heavy and not
particularly attractive,
but takes major abuse gracefully)
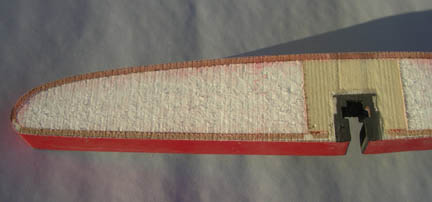 |
Current state-of-the-industry: EPS foam
core, inner glass, Divinycell, outer glass, paint. Fancier boards
substitute Carbon, and may throw in some veneer, but basically, this is what
most good Epoxy sandwich boards look like these days, be they surf,
windsurf, or kiteboards..
Observe the high-density Urethane block supporting the
fin box |
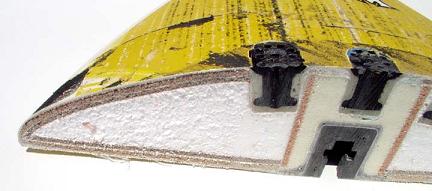 |
Double PVC sandwich for tough applications -
this one a JP high wind sailboard |
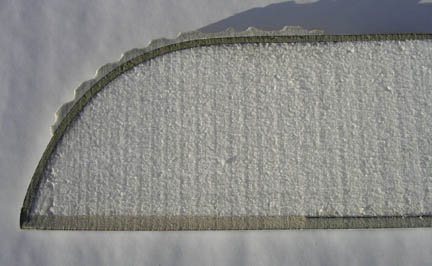 |
Nicely engineered custom Formula
windsurfing board: varying thickness and density sheet foam to match local
loads, Carbon reinforcements |
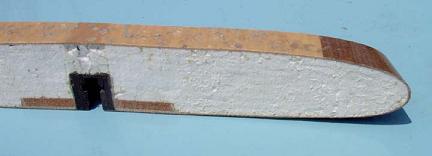 |
Surftech wood veneer board: EPS foam core,
inner glass, structural wood veneer. Strong and
gorgeous! |
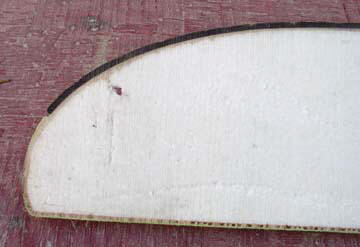 |
Honeycomb in the bottom, some sort of
Coremat-like stuff on the decks. These boards had enormous problems due to
the discontinuities produced by the snazzy recesses for padz and such |
And a few non-sandwich Epoxy boards |
 |
Economy construction: non-woven
fiberglass reinforcements (usually with a token unidirectional strand thrown
in someplace), with tough ASA skin. Ideal for rentals and such, but heavy
and lacking stiffness. |
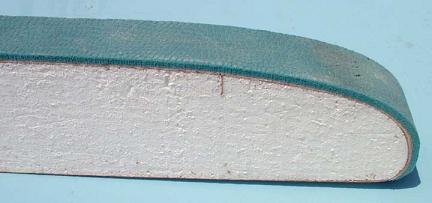 |
Surftech Softop. EVA foam padding
distributes deck loads, making for a fairly dent-resistant single-skin
construction. Strong and
tough while relatively light - favorites with rental places. |
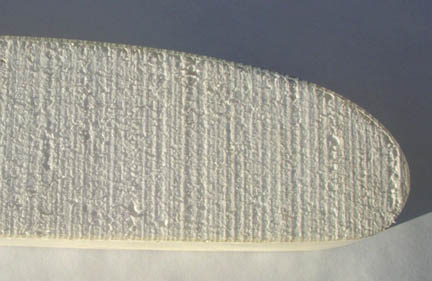 |
One of the many new single-skin
fiberglass over EPS core boards. I don't get it - all the extra cost and
vulnerabilities of Epoxy, with mechanical properties worse than the
old-fashioned glass board. At least those did not soak up water... |
|