Boards are stressed in many different ways: in "normal" operation, the
rider's weight pushes down, the ocean pushes back up, creating a bending
moment, often some torque as well, causing mostly compressive loads on deck,
and tension on the bottom. All sorts of bending/ twisting loads happen
during wipe-outs. And then there are encounters with hard objects, causing
impacts and punctures. The most common failure mode in old-fashioned "Glass
Boards", though, is denting. Single-skin construction, while strong overall,
has very little panel stiffness for its weight, leading to the
all-too-common creasing of glass boards over stringers, as well as deck
collapse under heels and toes.
Enter the sandwich: the same fiberglass skins one
would find in a comparable glass board, spaced apart by a relatively light
sheet foam, increasing the panel's stiffness many-fold. With such a
disproportionally large increase in panel stiffness, the core's density can
then be decreased, leading to an overall decrease in weight. Weight decrease
equals more float, better acceleration, and livelier turning due to lower
swing weight. An altogether most excellent improvement!
(btw, the boarding industry did not invent sandwich
construction - it came down to us from first the aircraft industry, later
all aspects of transportation - where lighter weight means higher profits.
Racing sailboats - my training ground - went sandwich in the early 70s and
never looked back)
So how does it work?
Below an example, using a few bits of paper, some EPS
foam, plus a couple chunks of lead:
|
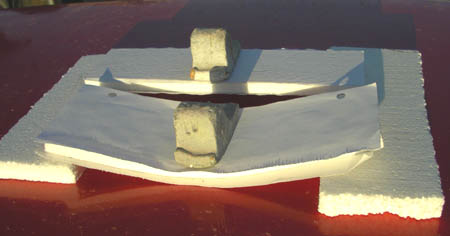 |
same exact ingredients as
above, but I glued the bits of paper to the bit of EPS foam with paper glue
- nothing fancy, just some Elmer's Glue-All. The loose stack in the
foreground, the glued one in back. What a
difference!! The glued up one hardly deflects at all, while the loose one is
bottomed out.
panel weight is identical for all intents and
purposes. |